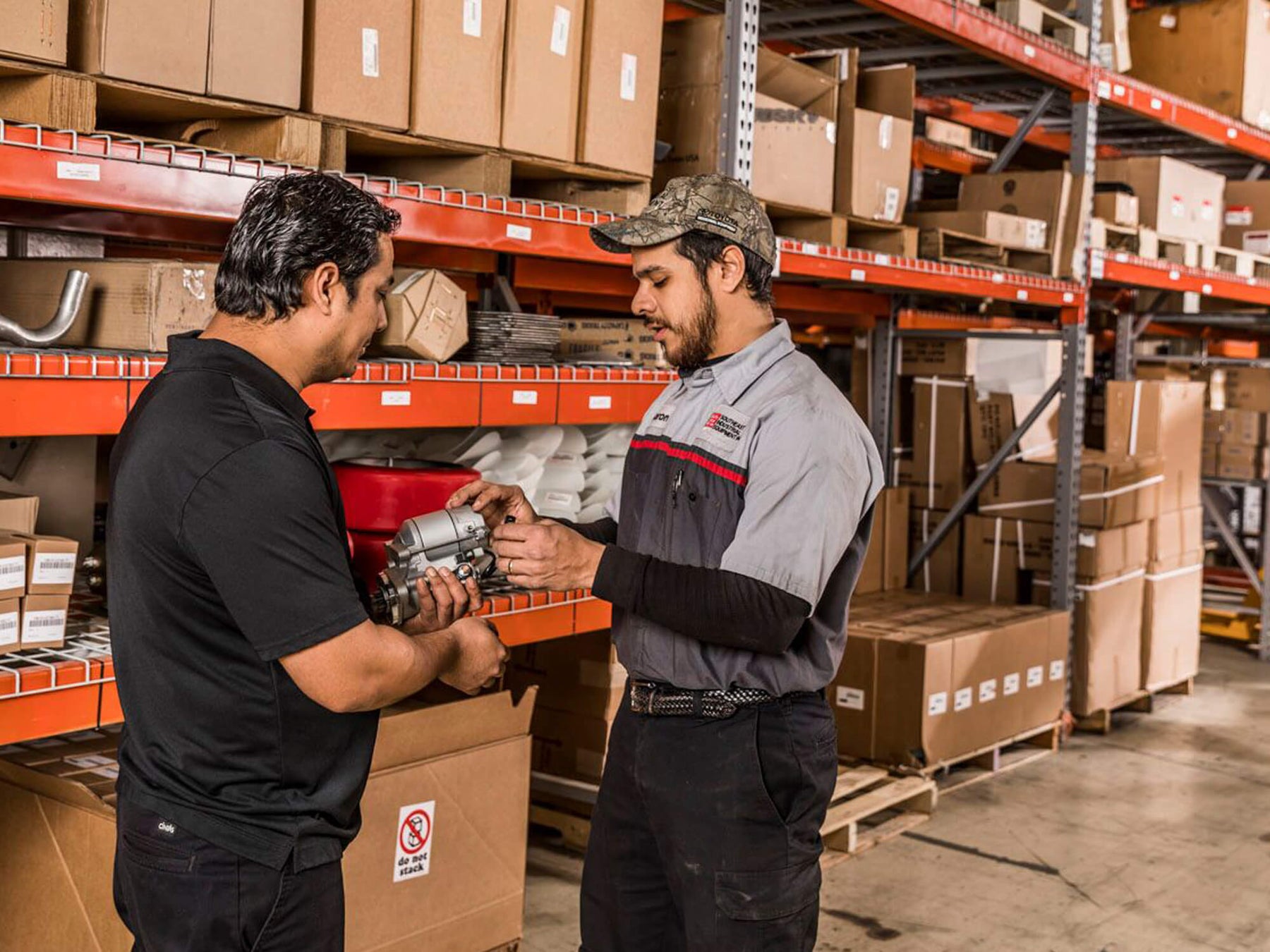
Critical Forklift Parts: What You Need to Keep Your Fleet Running Smoothly
In warehouse operations, every minute counts. Downtime caused by a malfunctioning forklift can disrupt workflows, delay shipments, and impact overall productivity. While maintaining a fleet of forklifts requires careful planning, one of the most effective ways to optimize uptime is by having the right forklift parts readily available.
At Liftow, we understand that not all forklift parts are created equal. Some components are essential for daily operations, while others can be replaced as needed. Knowing which forklift parts are critical can help your business stay ahead of potential disruptions while optimizing operational efficiency.
How to Determine Which Forklift Parts Are Critical?
Consider these key questions when determining which parts are critical:
-
What Parts Do You Replace Most Often?
Certain forklift components naturally experience more wear and tear due to daily use.
-
How Quickly Do You Need the Part?
If a forklift failure means immediate disruption to operations, that part is critical. However, if there is another forklift to cover the task, it would not be a critical spare part.
-
Will Operations Be Delayed Without It?
In case of an affirmative answer, it is a critical part.
-
What Is the Lead Time for the Replacement Part?
Understanding supplier lead times is essential for effective inventory planning. At Liftow, we help businesses optimize their spare parts strategy by offering quick access to a comprehensive inventory of forklift parts.
-
What Are the Repair and Replacement Timelines?
Working closely with a forklift service provider can help determine the best course of action.
Liftow offers an extensive inventory of forklift parts.
Stay Prepared
Stocking every spare part may not be practical, but strategic planning can help prevent extended downtime. Here are ways Liftow supports your operation:
-
Work with a Trusted Forklift Parts Supplier
Our experts can help identify the most critical parts based on your fleet size and operational requirements.
-
Optimize Your Forklift Service and Maintenance Plan
Routine maintenance can extend the lifespan of key components and reduce unexpected failures. Our forklift service plans include scheduled inspections and proactive part replacements.
-
Keep Emergency Contacts Readily Available
Having a direct line to a reliable forklift parts provider ensures that you can source necessary components without delay.
-
Consider a Forklift Rental as a Backup
In cases where a repair may take longer than expected, having access to forklift rentals can keep operations running smoothly.
Liftow offers flexible rental options for businesses that need temporary solutions while awaiting parts, and our forklift service plans include scheduled inspections and proactive part replacements.
Downtime is costly, but with the right strategy, it can be minimized. At Liftow, we provide end-to-end solutions to keep your operation running efficiently. From new and used forklifts to parts, rentals, and expert service, our team is dedicated to supporting your business with industry-leading expertise.
If you are looking for reliable forklift parts, expert maintenance, or fleet optimization solutions, we are here to help.
Contact Liftow today.
Liftow—Together, We Elevate Everything!
Leave a comment